Nach 2 Jahren Pause lockte Gütersloh International am 20. August 2022 bei bestem Sommerwetter sehr viele Menschen auf den Stadthallenvorplatz. Auch der AK Asyl Gütersloh hatte wieder einen der 38 Stände aufgebaut.
Geflüchtete und Arbeitskreis Mitglieder nahmen mit Hilfe von Finger-Fadenspielen Kontakt zu den Besuchern auf. Diese Fadenspiele sind weltweit bekannt. Spontan konnten sich viele ältere Menschen an die Geschicklichkeitsspiele aus ihrer Kindheit erinnern und ließen sich direkt auf eine Spielrunde ein. Aber auch Kinder trauten sich fasziniert und begeistert an das Abheben und Übergeben der Fäden heran. Das Ziel des Ak Asyl Gütersloh "Integration für Alle" wurde an diesem Nachmittag spielerisch und ohne Verständigungsschwierigkeiten umgesetzt.
Am Stand wurde selbstverständlich wie jedes Jahr auch Informationsmaterial zur aktuellen Flüchtlingssituation verteilt und gegen eine kleine Spende konnte man "Fäden" zum Weiterspielen mitnehmen.
Baumpflanzaktion im Bürgerwald
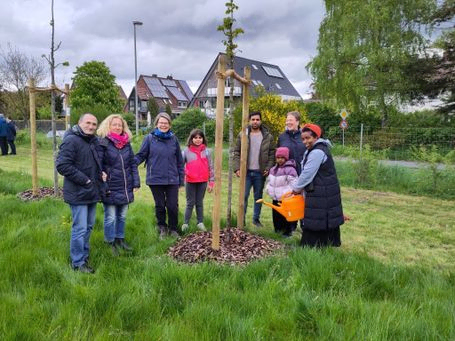
Baumpatenschaft
25 Geflüchtete aus Gütersloh haben einen Baum im Bürgerwald Gütersloh gespendet und am Samstag bei einem Pflanzfest an der Hollerstraße begossen.
Die Idee, als Mit- Bürger für die Gütersloher Stadtgesellschaft etwas beizutragen, entstand in einem von Elisabeth Meier gehaltenen Sprachkurs des AK Asyl. Die Akzeptanz für eine Spende war sofort groß. "Ein Beitrag für den Klimaschutz" meinte Habib aus Afghanistan. Und Dagmawit aus Eritrea verglich den jungen Baum, der seine Wurzeln in den Boden wachsen lässt, mit der Situation der Geflüchteten, die jetzt in Deutschland ihre Wurzeln schlagen, die wachsen, Blätter und - so hofft sie - Früchte tragen.
Stellvertretend für die 25 Spender fand sich eine kleine Gruppe an der Hollerstraße ein, wo die Bürgerstiftung das „Pflanzfest“ organisiert hatte.
Die Hopfenbuche ist einer der letzten Bäume, die gepflanzt wurden. Der Bürgerwald ist jetzt komplett und spiegelt mit seinen unterschiedlichen Baumarten und der großen Anzahl der Spender und Spenderinnen die Vielfalt der Gütersloher Stadtgesellschaft wider.
Im Juni soll dann auf der Wiese vor dem angehenden Wald mit allen Beteiligten ein Picknick veranstaltet werden."
Internationaler Sommerausflug zum MAXIMILIANPARK in Hamm
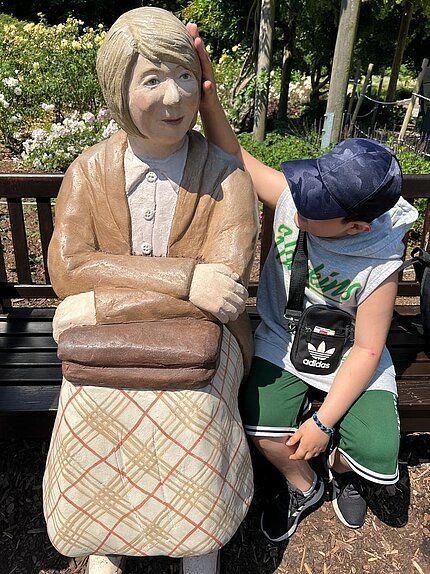
AK ASYL und Flüchtlingsberatung der Diakonie reisten am 24.06.2023 mit ca. 100 Gästen aus 13 verschiedenen Herkunftsländern zum Maximilianpark in Hamm.
Die Flüchtlingsberatung der Diakonie lud Geflüchtete, vorrangig Familien mit kleinen Kindern zu einem Sommerausflug ein. So hatten am 1. Feriensamstag fast 100 Personen aus 13 verschiedenen Nationen die Chance den Maximilianspark in Hamm zu besuchen.
Vorbereitet und begleitet wurde das Tagesprogramm von ehrenamtlichen Mitgliedern des AK ASYL der Ev. Kirchengemeinde Gütersloh.
Vor der Abfahrt der Busse, die um 10.00 Uhr vom Marktplatz aus starteten, wurde Proviant verteilt. Alle erhielten für ihre Taschen oder Rucksäcke Wasserflaschen, Brezeln und Äpfel. Ein Bollerwagen wurde ebenfalls verladen. Dieser transportierte weitere Ausrüstung und markierte später im Park den Treffpunkt.
Der „Maximilianpark,“ angelegt anlässlich der 1. Landesgartenschau 1984 auf dem Gelände der ehemaligen Zeche Maximilian ist heute ein attraktiver Park mit spannenden Angeboten für Jung und Alt.
Nicht nur Familien mit Kindern konnten an diesem Tag entspannte Stunden bei wunderschönem Sommerwetter verbringen. Der Wasserspielplatz war ideal zum Matschen für die Kleinen. Aber auch Klettern, Balancieren, Rutschen und all das, was die vielen unterschiedlichen Themenspielplätze anboten, ließ die Zeit schnell vergehen.
Zwischendurch gab es Führungen im Schmetterlingshaus, das mit mehr als 80 verschiedenen Schmetterlingsarten, Wasserschildkröten und Insekten in einem tropischen Klima beeindruckte.
Einige erkundeten den „Gläsernen Elefanten“, blickten auf das Parkgelände von oben und schauten sich in der Ausstellung „Die 3. Dimension“ teils skurrile Objekte an.
Zum Glück gab es auch größere schattenspendende Bäume, so dass trotz der Wärme ein Spaziergang durch das Parkgelände angenehm war. Eine enorme Anzahl an unterschiedlichen Stauden und Gräsern erfreute besonders die erwachsenen Gartenliebhaber.
Auf dem Rückweg nach Gütersloh war es recht still im Bus. Die Kinder waren „geschafft“ und verschliefen teilweise die Rückfahrt. Viele der ukrainischen Mitfahrenden schauten allerdings auf ihre Handys und informierten sich über die neuesten Nachrichten zum Kriegsverlauf in ihrer Heimat. So erfuhren sie, dass die „Wagnertruppe“ sich auf den Weg nach Moskau gemacht hatte und kamen viel zu schnell und erschrocken wieder im Alltag an.
Hoffentlich können trotzdem alle von diesem erlebnisreichen Ausflugstag zehren, den sie dankbar genossen haben.
Großzügige zweckgebundener Spenden, die der AK ASYL der Ev. Kirchengemeinde im vergangenen Jahr erhielt, machten diesen besonderen Sommertag möglich. Kultur -und Freizeitangebote sollten hier lebende geflüchtete Menschen erreichen. Die Spenden sollten den Geflüchteten ermöglichen, das Leben in Deutschland auch außerhalb der Flüchtlingsunterkünfte kennenzulernen. Das ist auf jeden Fall gelungen!
DANKE – SHUKRAN – FALEMINDERET – MERCI - GRAZIA
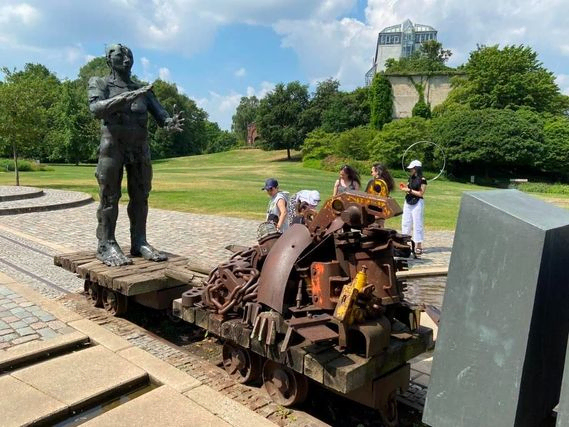
Gütersloh International 2022
Ausflug zum Zoo nach Osnabrück
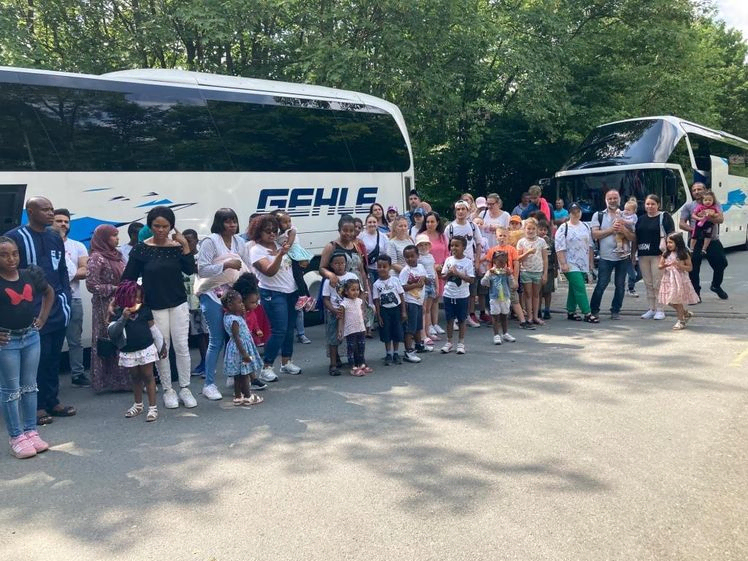
Dank einer großzügigen Spende der AZ DIREKT GmbH konnte der AK Asyl für in Gütersloh lebende Geflüchtete einen Tagesausflug organisieren. Mit 2 Bussen starteten am 4. Juli morgens 45 Erwachsene (davon 6 ehrenamtliche Begleitende) mit 45 Kinder zum Zoo nach Osnabrück. Ein Picknick mit internationalen Spezialitäten ergänzte den Zoobesuch. So wurde es ein besonderer gelungener Ferientag mit einer guten Stimmung bei allen Teilnehmern, die aus 11 verschiedenen Ländern kamen.
Erdbeeren: Pflücken, Verarbeiten und Genießen
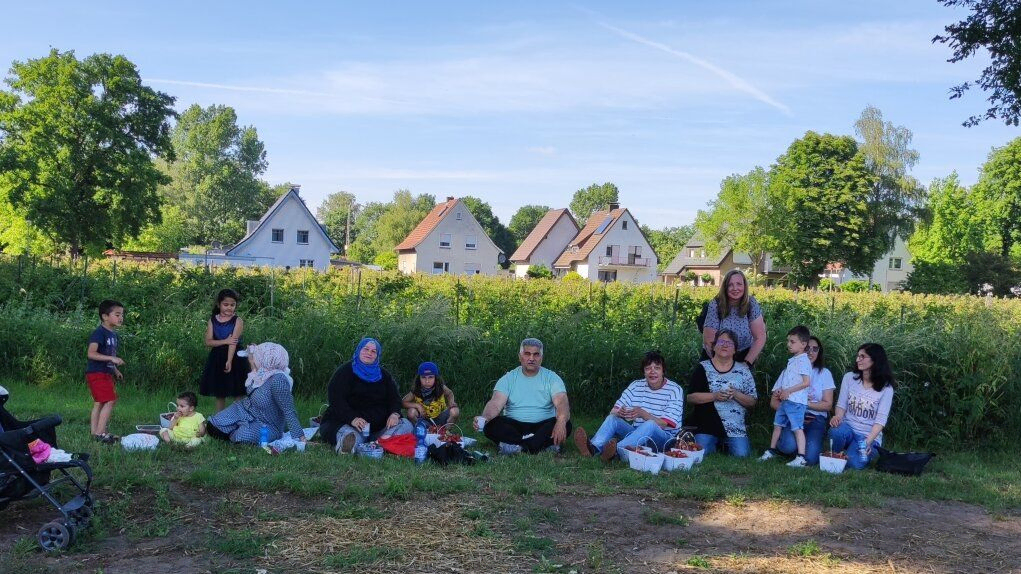
Passend zur Erdbeerzeit im Juni trafen sich an 3 Nachmittagen Geflüchtete und ehrenamtliche Begleiter im Café Connect bzw. auf dem Erdbeerfeld am Hof Schröder. Das gemeinsame Pflücken, Verarbeiten und anschließende Genießen der frischen Früchte und der köstlichen Marmeladen machte allen Beteiligten viel Spaß und förderte die interkulturelle Begegnung. Außerdem konnten die Deutschkenntnisse unserer Neubürger eifrig erprobt oder auch flüsssig angewendet werden.
Energiesparen und Umweltschutz – Geflüchtete erwerben Zertifikat im Café Connect
„Ich habe heute viel Interessantes gelernt, herzlichen Dank!“, so das Fazit einer jungen Irakerin am Ende der Veranstaltung. Ernst-Jürgen Michaelis, Integrationsbeauftragter der Stadt Rheda-Wiedenbrück war einer Einladung des Evangelischen Kirchenkreises Gütersloh und des Arbeitskreises Asyl der Evangelischen Kirchengemeinde Gütersloh und der Diakonie gefolgt: Er referierte im Café Connect zum Thema Energiesparen und Umweltschutz vor etwa 20 Geflüchteten, die unter anderem aus Afghanistan, Irak und Syrien stammten. Er verstand es, mit einer Mischung aus Vortrag, Kurzfilmen und praktischen Übungen sein Publikum zu begeistern. „Stellen Sie sich vor, Sie haben eine eigene Wohnung und müssen alle Nebenkosten selber zahlen, da kommt einiges zusammen. Und mit einfachen Tipps können Sie eine Menge Geld sparen und gleichzeitig das Klima schützen!“, so der 62-Jährige. Beim Thema Mülltrennung gab es eine praktische Aufgabe. „Keine Angst, der Müll hier ist ganz sauber! Aber was gehört wohin?“ fragte Michaelis die Teilnehmenden. Zielsicher sortierten die Geflüchteten daraufhin den mitgebrachten Abfall nach Restmüll, Papier, Gelber Sack, Altglas, Biomüll und Elektroschrott. Die Veranstaltung endete nach etwa drei Stunden. Die Zertifikate stehen in einigen Tagen zur Verfügung. Sie sollen insbesondere bei der Wohnungssuche helfen und Vermietern zeigen, dass die zukünftigen Mieter und Mieterinnen wissen, wie man mit Energie und Abfall richtig umgeht.
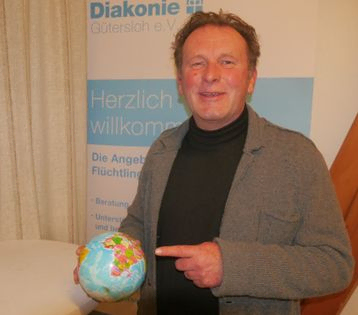
Erläuterte Umweltschutz auf anschauliche Weise: Ernst-Jürgen Michaelis, Integrationsbeauftragter der Stadt Rheda-Wiedenbrück.
Text & Foto: Dr. Gunnar Waesch
Flüchtlingsberatung der Diakonie Gütersloh organisierte Ausflug nach Detmold
Zum Auftakt der Ferien hat die Flüchtlingsberatung der Diakonie Gütersloh einen Tagesausflug ins LWL-Freilichtmuseum Detmold organisiert. 35 Erwachsene und 45 Kinder waren mit von der Landpartie; neben geflüchteten Menschen auch einige Patinnen und Paten. In zwei Bussen machte sich die Gruppe auf zum größten Freilichtmuseum Deutschlands.
Dort, am Fuß des Teutoburger Waldes, konnten sie sehen, wie die Landschaft in Westfalen noch vor Jahrhunderten aussah. Außerdem erfuhren sie, wie die Menschen damals lebten und arbeiteten. An Wiesen und Feldern entlang führte der Rundweg zu einzelnen Dörfern mit Höfen und anderen historischen Gebäuden aus fünf Jahrhunderten, darunter Bauernhäuser mit Gärten voller Kräuter und Gemüse, eine alte Schule und eine Bockwindmühle. Das Haupthaus des Münsterländer Gräftenhofes – der größte Hof auf dem Gelände – war erst kurz zuvor umgestaltet und wieder für Besucher geöffnet worden.
„Was ist das?“ „Wie heißt das?“ „Kann man das essen?“, fragten die Kinder immer wieder. Sie freuten sich, dass sie vieles anfassen und selbst ausprobieren durften. Besonders fasziniert zeigten sie sich von den riesigen Scheunen und den alten Haustierrassen, wie den Bentheimer Schweinen und Landschafen, den Lippegänsen oder auch den Senner Pferden. Diese gelten als die älteste Pferderasse Deutschlands.
Einige der geflüchteten Menschen trafen Vergleiche mit der verlorenen Heimat: „Ich hatte früher auch so ein Kornfeld“, sagte eine jesidische Frau und fügte nachdenklich hinzu: „Jetzt leider nicht mehr.“ Andere erinnerten sich daran, dass ihre eigene Mutter oder Großmutter noch spinnen und weben konnte. „Für uns war es erstaunlich und auch sehr positiv zu sehen, wie sich die geflüchteten Menschen im Freilichtmuseum mit dem Thema Heimat befasst haben“, sagte Katharina Stein von der Flüchtlingsberatung der Diakonie Gütersloh. „Und ich freue mich sehr darüber, dass auch unsere Paten so viel Freude an dem Ausflug hatten.“
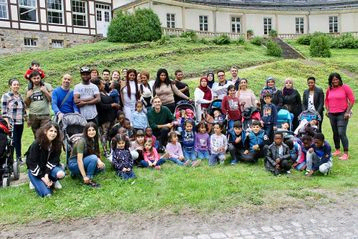
Ausflug ins Freilichtmuseum Detmold mit der Flüchtlingsberatung der Diakonie Gütersloh: 35 Erwachsene und 45 Kinder genossen den Erlebnis- und lehrreichen Tag.
Auf nach Münster!
Über den AK Asyl organisiert bieten wir ehrenamtlich seit fast 4 Jahren morgens Deutschunterricht für geflüchtete Menschen auf verschiedenen Niveaustufen an. Einige unserer Sprachschüler und Sprachschülerinnen kommen bereits über mehrere Jahre regelmäßig zum Unterricht in die Kirchstraße. In der Fortgeschrittenengruppe überlegten sich die SchülerInnen und ihre 3 Lehrerinnen, einmal zum Abschluss kurz vor den Sommerferien einen Besuch in der Stadt Münster zu machen
Wir beschlossen mit dem Zug zu fahren und an einer Stadtführung teilzunehmen.
Dank Spendengeldern waren die Kosten für die 9:00 Uhr Tickets und für die Stadtführung gedeckt, so konnten wir weiterplanen.
Am Mittwoch den 3. Juli war es dann soweit.
Die Stadtführerin der „Stadtlupe“ - so der Name der Organisation – holte uns am Bahnhof ab und los ging es. Schon beim Passieren des Lackmuseums mit seiner roten Lacktreppe gerieten einige ins Staunen!
Unser erster Halt: die Promenade mit ihren grünen Linden und den vielen Fahrrädern! Etwas langsamer gesprochen als üblich startete die Führerin ihre Erklärungen zur Anlage der Stadt, zur Entstehung der Stadt und dann zu Münsters Lieblingsfortbewegungsmittel: dem Fahrrad. Davon fahren in der Stadt etwa 500 000. Es gibt also doppelt so viele Zweiräder wie Einwohner in der Stadt.
Ein Abstecher in die Clemenskirche, die um 1750 vom bedeutendsten Baumeister Münsters Johann Conrad Schlaun erbaut wurde, folgte. Dem begegneten wir dann gleich wieder beim Bestaunen des Erbdrostenhofes. Die Allegorischen Monatsnamen an der Fassade waren gut zu erkennen. Einen Sprung weiter tauchten wir in moderne Kunst ein. Das Foucaultsche Pendel mit den Spiegelfassaden von Gerhard Richter an der Dominikanerkirche bildete einen unerwarteten Kontrast.
Der Gang führte an den Käfigen der Wiedertäufer an den Lamberti Türmen vorbei zum Dom. Es war Markttag. Herrlich viele bunte Stände mit reichlichen Angeboten waren zu bestaunen. Exakt zu 12:00 standen wir vor der Astronomischen Uhr, deren Figuren sich – zum Erstaunen aller, bewegten, vorbeizogen und wieder verschwanden. Klein Jonas, den Zoreh dabeihatte, war völlig fasziniert. Im „Paradies“, so wird die Eingangshalle des Doms in Münster genannt, wurden noch die Figuren erklärt und ebenfalls Fotos vom im Krieg völlig zerstörten Münster gezeigt. ( egränzen? Dabei kamen teilweise auch Erinnerungen an die zerstörten Heimatstädte. )
Den Abschluss des Rundganges bildete ein kurzer Besuch im Friedenssaal, wo wir von der Geschichte des 30jährigen Krieges, seinen Folgen und den Friedensbemühungen hörten.
Im Innenhof des Landesmuseums machten wir dann gemeinsam eine kleine Pause, bevor die Gruppe sich aufteilte und Münster mit seinen Parks und Geschäften auf eigene Faust erkundete.
Zur Rückfahrt gegen 17:00 trafen sich alle wieder im schön renovierten Bahnhof, um den Heimweg anzutreten.
Müde von vielen Eindrücken, aber auch sehr zufrieden mit einem interessanten Tag kehrten wir alle nach Gütersloh zurück.
Projekt "Filzen verbindet"
Pfarrerin Kerstin Jacobsen und Sozialpädagogin Mariyam Hüser-Granzow haben sich im Café Connect mit einheimischen und Flüchtlingsfrauen getroffen, um gemeinsam zu filzen und dabei ins Gespräch zu kommen.
Aus den Arbeiten, in denen auch persönliche Erfahrungen zum Ausdruck kommen, soll nun ein Wandteppich gebildet, im Café aufgehängt und vielleicht auch anderswo gezeigt werden.
Dieses Projekt wurde mit 1000,-€ über die Evangelische Stiftung gefördert. Die Spendenübergabe fand am 7. Juni im Rahmen einer Feierstunde im Café Connect statt. Insgesamt wurden bei dieser alljährlichen "Ausschüttung" 20.000,- € für verschiedene soziale und kirchliche Projekte verteilt.
Newroz 2019
Newroz oder Nowruz, bzw. türkisch Nevruz (übersetzt „Neuer Tag“) ist der Name des persischen Neujahrs- und Frühlingsfestes. Schon mehrmals wurde über die Flüchtlingsberatung organisiert dieses Fest gemeinsam mit Gästen aus unterschiedlichen Nationalitäten und Religionsgemeinschaften auf dem Gelände des Hauses der Kirche gefeiert.
Aktion - Müllsammeln
Seit September 2014 wohnen im Kolpinghaus an der Kolpingstraße geflüchtete Menschen aus den verschiedensten Kriegs- und Krisengebieten. Sie werden von der Stadt Gütersloh und ehrenamtlich von Mitgliedern der Kolpingsfamilie Gütersloh-Zentral sowie des Arbeitskreises Asyl betreut.
Etliche Bewohner sind inzwischen gut in Gütersloh angekommen. Bei den wöchentlichen Montagstreffen mit den ehrenamtlichen Helfern haben sie überlegt, was sie für das Gemeinwohl der Menschen vor Ort tun können. Da wuchs die Idee, entlang der Dalke Müll aufzusammeln. In Absprache mit Herrn Gaerdes vom Umweltamt der Stadt Gütersloh, der Handschuhe, Warnwesten, Zangen und Abfallsäcke zur Verfügung stellte, konnte die Aktion starten.
Am letzten Samstag sammelten neun Bewohner und vier Helfer von der Neuen Mühle bis zu den Berufsschulen den Unrat ein. Alle waren froh, dass der eisige Ostwind, der Tage vorher wehte, nachgelassen hatte. Es war erstaunlich was so alles gefunden wurde: viele Flaschen, Brötchentüten, Bonbonpapier, Handschuhe, einen einzelnen Hausschuh, einen Teil eines Kinderautositzes, viele Zigarettenkippen und sogar ein Portemonnaie mit Ausweispapieren und Bankkarten. Nach der gelungenen Aktion, bei der sechs große Säcke Müll gesammelt wurden, gab es ein gemeinsames Mittagessen im Pfarrheim St. Pankratius.
(Bericht aus der NW vom 7. März 2018)
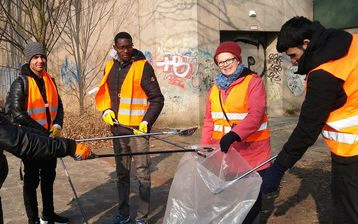
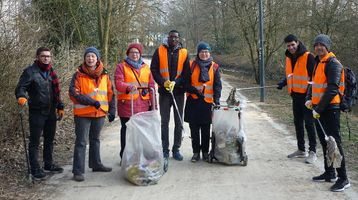